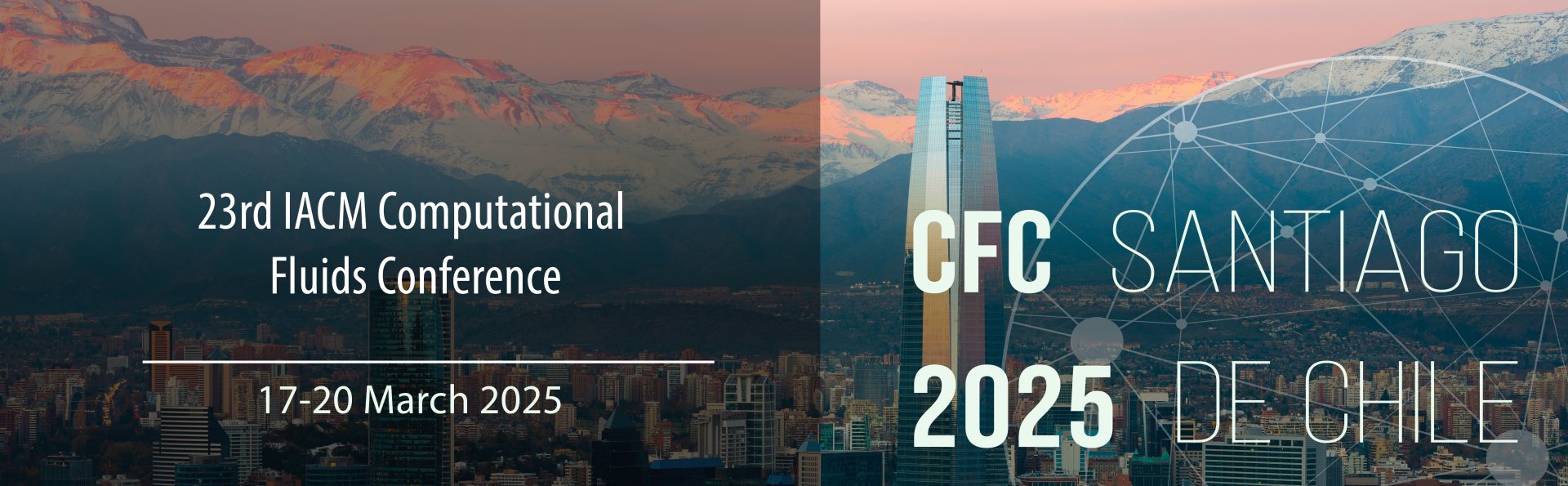
A temperature reconstruction framework for food freezing process in mixed turbulent flows by FV-URANS forward simulations and data assimilation techniques with optimal sensor placements
Please login to view abstract download link
The description of food freezing dynamics in refrigeration cabinets plays a crucial role in the energy-efficient control of refrigeration equipment and in the final quality of the frozen foods. However, forward time-dependent modelling of nonlinear coupled phenomena such as solid-liquid phase change and turbulent airflow is computationally demanding. Moreover, direct food measurements are undesirable as they are invasive and difficult [1]. Recently, data assimilation techniques have allowed to precisely estimate spatial and temporal fields with low computational cost by using limited or noisy measurements and a reduced dimensionality model [2]. In this work, we propose a temperature reconstruction framework for the freezing process of a salmon slab in a convective freezer cabinet consisting of: (1) A Finite Volume solver with the k-ω SST URANS model for the turbulent airflow, and the effective heat-capacity method for the phase-changing food. Also, third-order WENO and optimized-BDF2 schemes are used for spatial and time approximations, respectively. (2) A SVD regularized least-squares recovery approach that utilizes a reduced-order space constructed by a five-dimensional parameter set from the forward model and low-quality artificial measurements. Optimal sensor placements in the domain are compared for thermo-camera measurements, for non-invasive measurements, and for three different greedy algorithms based on a-priori error estimation. Our framework demonstrated a significant reduction in computational load while ensuring accurate local temperature monitoring during the freezing process. The greedy approach proved efficient in identifying sensor locations that maximized data representativeness, allowing a reduction from 352 to 56 sensors while maitaing an error close to 1%.