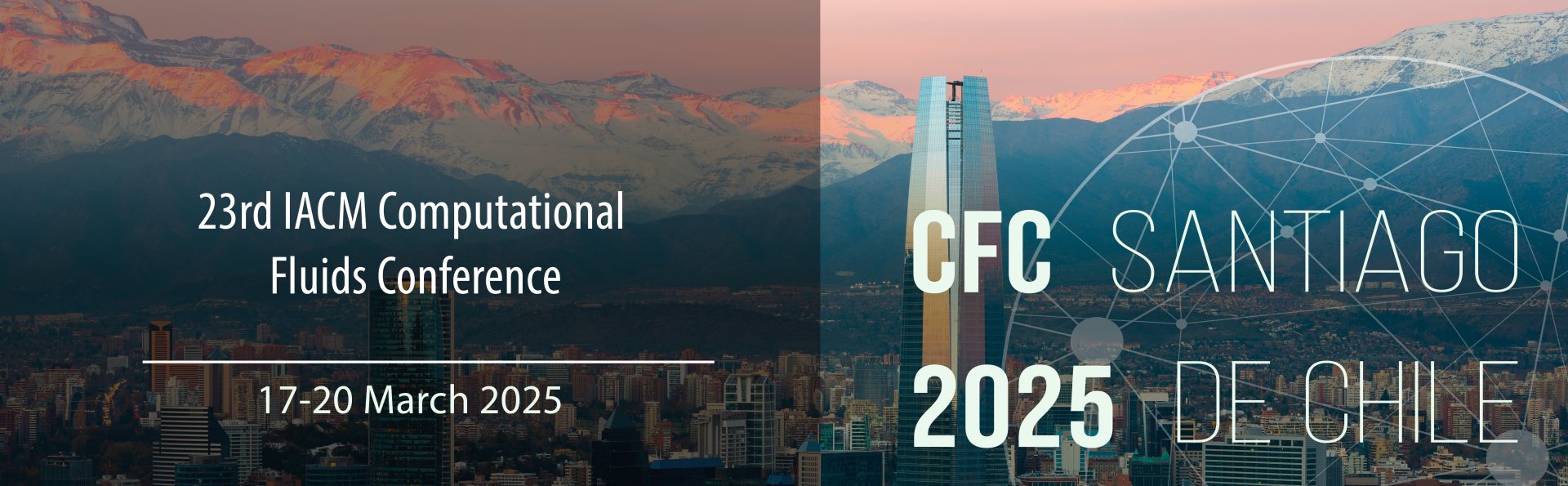
Modeling, Simulation, and Optimization in Manufacturing: Selected Applications in Lubricated Orthogonal Cutting and Extrusion
Please login to view abstract download link
Designing manufacturing processes to achieve the desired production accuracy often remains a trial-and-error endeavor. This is largely due to the complexity of the underlying phenomena, which can exceed engineering intuition, and the limited formal understanding of these processes. In this talk, we will explore two manufacturing applications where modeling, simulation, and optimization significantly enhance process performance: lubricated orthogonal cutting and static mixers for extruders. In orthogonal cutting, reliably predicting the coefficient of friction between the tool, chip, and workpiece is critical for ensuring a cost-effective and dependable process. Current numerical methods frequently rely on homogenized approaches that assume constant friction coefficients, failing to account for local effects. Moreover, the influence of lubricants and the local topographies of the tool and chip are often overlooked. To address these gaps, we introduce a micro-scale friction model that can be coupled with a meso-scale chip formation model. The micro model calculates a localized friction coefficient based on factors such as temperature, contact pressure, cutting speed, and wetting by the used lubricant. It also incorporates experimentally determined tool and chip topographies, enabling a more accurate and detailed representation of the frictional behavior. In plastics profile extrusion, static mixers are positioned before the extrusion die to achieve a thermally and materially homogeneous melt flow. The design of these mixers involves a multi-objective optimization: maximizing mixing efficiency while minimizing pressure loss. We present an optimization method that employs boundary-conforming, spline-based lattice structures, a low-dimensional parameterization of these structures, and a trust-region optimization algorithm. For both applications, isogeometric analysis and reduced-order modeling are pivotal in significantly reducing computational effort, enabling more efficient and effective design optimization.