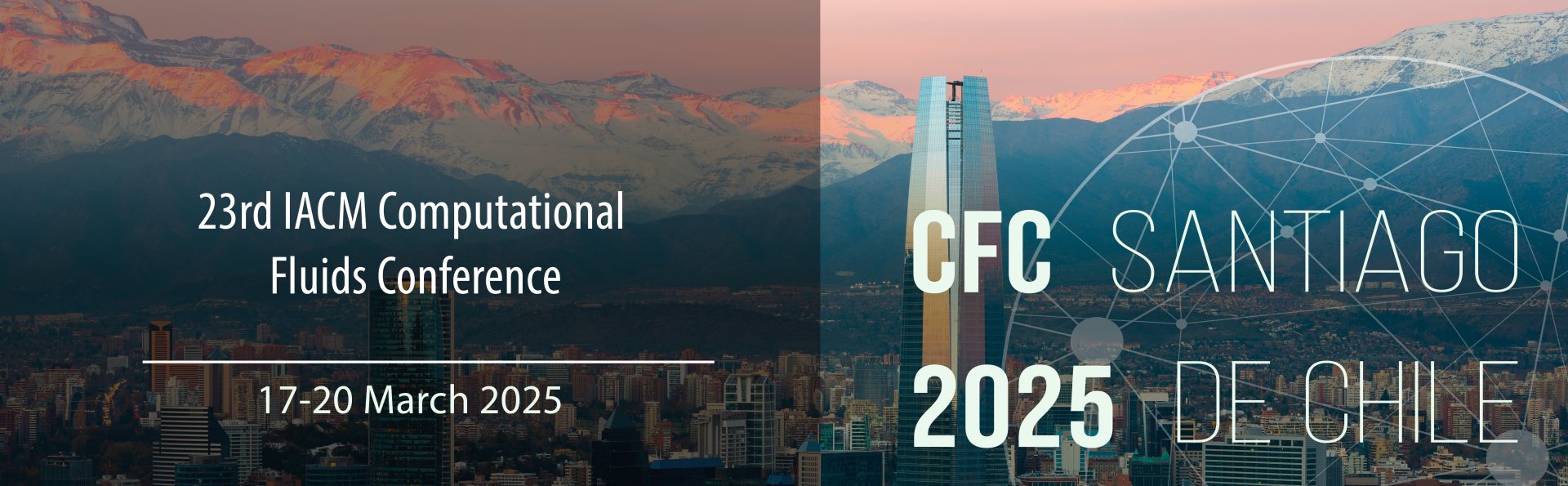
Thermofluid Simulation of Single-Strand Deposition in the Context of FDM 4D Printing
Please login to view abstract download link
In this study, we present a numerical investigation of single-strand deposition during 4D printing based on Fused Deposition Modeling (FDM). The shape-shifting property is achieved by programming residual stresses during the printing process, which are later released when the temperature exceeds the glass transition threshold. We aim to explore the stress programming mechanism and its dependence on key printing parameters, such as cooling rate, nozzle temperature, printing speed, and print gap. Accurately quantifying the effect of these factors is essential for reliably predicting the shape-morphing behavior of the final structure. The high-fidelity numerical model employed in this work solves the thermofluid fields using the stabilized finite element method combined with the arbitrary Eulerian-Lagrangian formulation. A boundary-conforming approach is used to accurately track the strand surface [1]. The mesh motion is enhanced by the surface-reconstruction virtual-region method [2], which is designed to handle the large displacements of the strand during deposition. The Cross-WLF viscosity model is used to characterize the shear-thinning and the temperature-dependent behavior of the polymer material. Results of thermofluid fields and programming forces under different process parameters will be presented and discussed. [1] González FA, Elgeti S, Behr M, Auricchio F. A deforming-mesh finite-element approach applied to the large-translation and free-surface scenario of fused deposition modeling. Int J Numer Meth Fluids, 95(2): 334–351, 2022. [2] González FA, Elgeti S, Behr M, The surface-reconstruction virtual-region mesh update method for problems with topology changes. Int J Numer Methods Eng. , 124(9): 2050–2067, 2023.