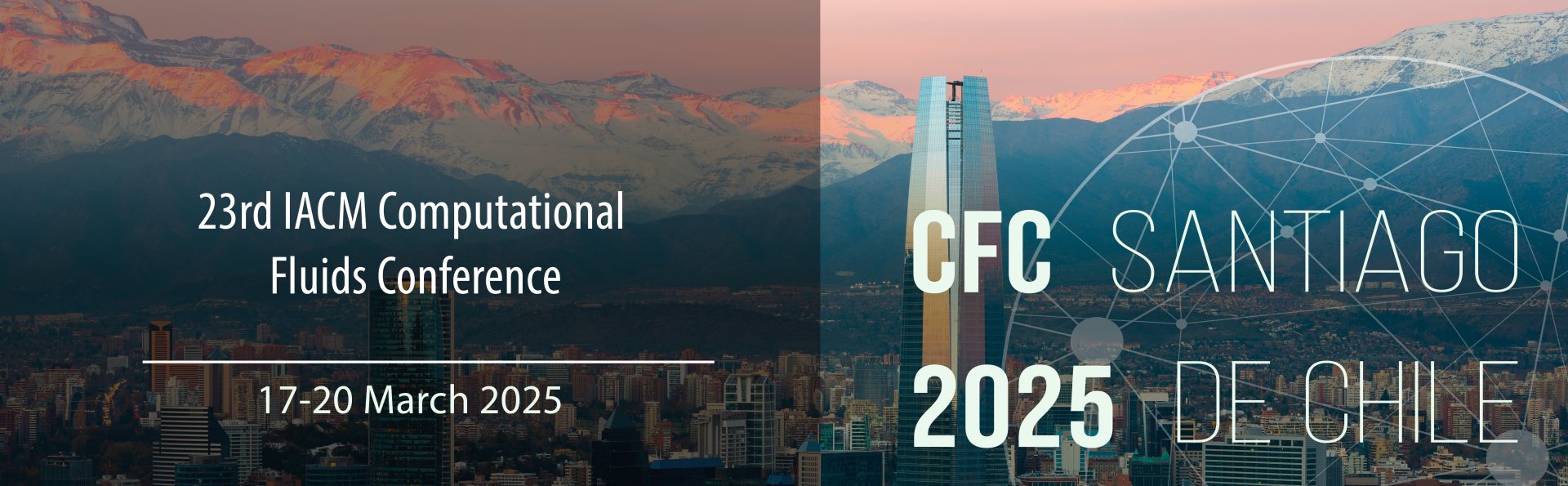
Simulation of open channel flow and rotating sliding mesh with open source CFD code CAFFA3D
Please login to view abstract download link
The open source and freely available fluid flow solver \textit{CAFFA3D} \cite{Usera2008} was adapted to simulate the performance of a medium-scale Hydrostatic Pressure Machine (HPM) with straight radial blades, introduced by \cite{Senior}. In order to simulate open channel flows, \textit{CAFFA3D} implements the VOF (Volume of Fluid) method \cite{Hirt} with CICSAM technique for the calculation of flow across cell's boundaries \cite{Ubbink} and an estimation of surface tension forces \cite{Brackbill}. To model a rotating device in \textit{CAFFA3D}, such a hydropower turbine or water wheel, the computational domain is divided in stationary and rotary block meshes. The rotation of the moving blocks is obtained by trigonometric relationships and the communication across the interface bewteen stationary and moving blocks is treated with the Sliding Mesh (SM) technique \cite{Usera2008}. The implementations of these methods were validated against previous experimental and numerical tests found in the literature. The Power--Discharge and Efficiency--Discharge curves obtained from the simulations presented a good correlation with the experimental curves, up to the discharge value corresponding to the maximum power of the HPM \cite{Pienika}.