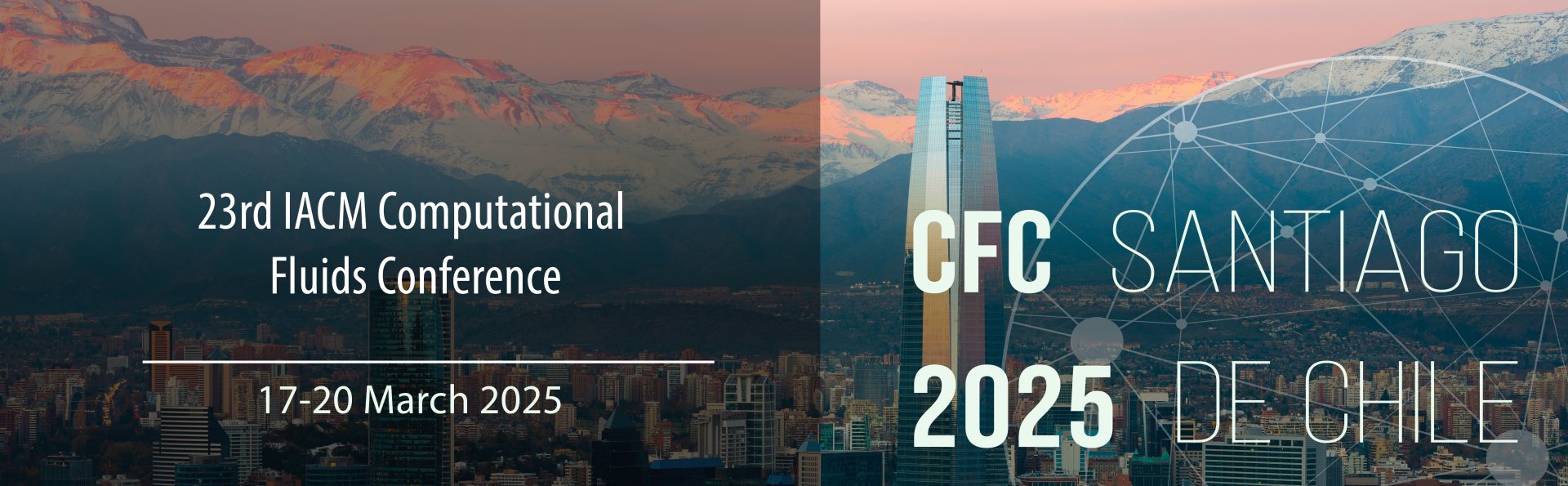
3D Numerical prototyping of universal droplet generators
Please login to view abstract download link
Numerical simulations are crucial for designing and optimizing devices that generate micro-droplets by dispersing one fluid (dispersed phase) into another (continuous phase). These droplets are key elements in various applications, including drug delivery, material synthesis, and cell isolation among others. The study of the operating conditions required for experimental production of micro-droplets in two-phase systems continues to advance, driven by the need to understand critical parameters to obtain the different possible regimes. In this study, we explore three types of micro-droplet generators, covering nearly the entire spectrum of technologies available in the literature. Simulations were performed for coaxial generators in 2D and for T-junction and X-junction geometries for square and circular cross sections in 3D. Coaxial generators are well-suited for high-throughput applications and can rely on axial symmetry for simplified modeling. In contrast, T-junction and X-junction devices are more versatile, widely used in microfluidic laboratories, and commercially available in materials such as PEEK (Polyetheretherketone) for liquid chromatography and related applications. These geometries, however, pose unique challenges for simulation, as assumptions like axial symmetry or conformal domains are not applicable. To address these challenges, those 3D simulations were developed using an embedded boundary method, which defines the capillaries’ shapes within a Cartesian mesh. This approach captures the fluid interface dynamics with high precision. Basilisk, an open-source software designed for solving flow equations using the volume-of-fluid method, was utilized. Its ability to calculate curvature and surface stresses efficiently makes it ideal for simulating two-phase flows in microfluidic systems. The results include a computational analysis of droplet formation in the three different systems, comparing with experimental data from the literature. The findings validate the numerical model, offering insights into optimizing operating conditions to control droplet size and generation frequency. This work highlights the value of numerical simulations in advancing microfluidic device design, supporting their use in both research and industry.