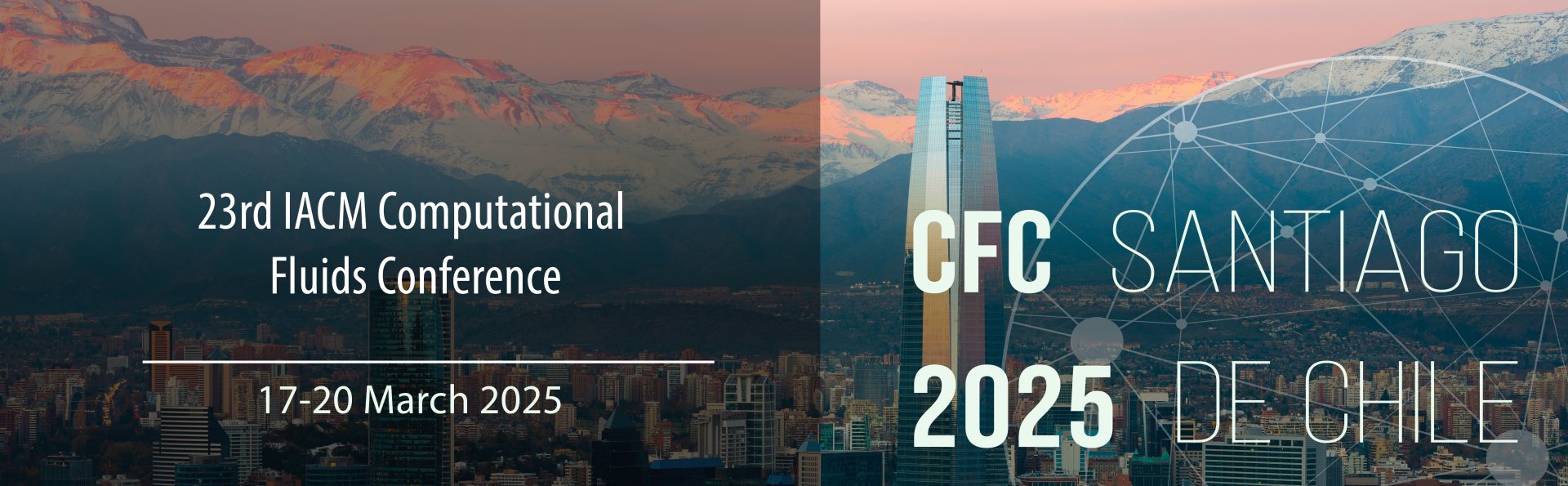
Numerical Simulation of a Fume Treatment Filter System
Please login to view abstract download link
Fume Treatment Centers (FTC) are essential for the operation of anode baking furnaces and for keeping emissions within environmental limits. Many FTCs in operation today have exceeded their initial design life and, due to creeping process, also the initial design operational conditions. One important issue regarding with this situation is how the fume flow behavior could be improved and optimized. Mainly due to the anode production increase, the required increase in the fumes flow coming from the furnace impact directly on filter bag life, process operation condition, bag cleaning sequences, localized metallic erosion in filters cages, etc. The objective of this study is the numerical simulation in ANSYS Fluent of the flow in a fume treatment filtration system using sleeve filters. In the initial phase of this study, the filter fabric was characterized as a "porous jump" for the numerical model based on experimental data obtained from the literature, for both "clean" and "dirty" conditions. A single cylindrical sleeve filter was then studied under operating flow to evaluate the pressure distribution on the filter and the total pressure drop produced in the system, considering that most particle accumulation occurs at the end of the sleeve. Finally, a complete model of a set of 4 filtration boxes, with approximately 1200 sleeve filters, was constructed. The model allows for the calculation of stresses on each filter. Flow velocity and pressure distributions in the filtration boxes were analyzed to identify areas where the filters are subjected to more severe conditions and to propose design improvements.